ความปลอดภัยและสภาพแวดล้อมในการทำงาน
ระบบบริหารจัดการด้านความปลอดภัย อาชีวอนามัยและสิ่งแวดล้อมองค์กร
พีทีจี จัดทำระบบมาตรฐานผลิตภัณฑ์อุตสาหกรรม โดยจะดำเนินการจัดการแบบบูรณาการ (Integrated Management System) ทั้ง 3 ระบบเข้าด้วยกัน ซึ่งจะเรียกว่า "ระบบการจัดการ" ตามมาตรฐานมอก. 9001-2559, ISO 9001: 2015 Quality Management Systems Requirement มอก. 14001-2515, ISO 14001: 2015: Environmental Management System Requirements และ มอก. 45001-2518, ISO 45001: 2018 Occupational Health and Safety Management System
ในการบริหารจัดการอาชีวอนามัยและความปลอดภัยภายในองค์กร บริษัทได้กำหนดนโยบายคุณภาพ ความมั่นคง ความปลอดภัย และสิ่งแวดล้อม (Quality, Security, Occupational Health and Safety, Environmental Policy: QSSHE) ขึ้น เพื่อดูแลควบคุมกระบวนการปฏิบัติงาน การปรับปรุงการให้บริการ การเพิ่มผลผลิต (Productivity Improvement) ให้ดียิ่งขึ้นอย่างต่อเนื่อง (Continuous Improvement) เพื่อให้ผู้ปฏิบัติงานเกิดความตระหนักในการปฏิบัติการเพื่อจัดการความเสี่ยงและโอกาสด้าน QSSHE ขององค์กร รวมถึงผู้มีส่วนได้เสีย (Stakeholders) ทุกกลุ่ม
นอกจากการใช้มาตรฐานสากลในการบริหารจัดการทางด้านความมั่นคง ความปลอดภัย อาชีวอนามัยและสิ่งแวดล้อมแล้ว เพื่อให้มั่นใจว่าทุกหน่วยธุรกิจจะนำมาตรฐานความมั่นคง ความปลอดภัย อาชีวอนามัยและสิ่งแวดล้อม ไปเป็นส่วนหนึ่งของการดำเนินธุรกิจ บริษัทฯ ได้จัดทำระบบมาตรฐานความมั่นคง ความปลอดภัย อาขีวอนามัยและสิ่งแวดล้อม กลุ่มบริษัท PTG ( PTG SSHEMS) โดยมีวัตถุประสงค์เพื่อกำกับดูแลมาตรฐานการบริหารจัดการความมั่นคง ความปลอดภัย อาชีวอนามัยและสิ่งแวดล้อม ให้เป็นระบบเดียวกันทั่วทั้งองค์กรเป็นอย่างต่ำ โดยเป้าหมายของระบบ
PTG SSHEMS มุ่งให้เกิด
ㆍZero Accident
ㆍZero Environmental Claim
ㆍZero Security Incident
ㆍZero Process Safety Event
ระบบได้ดำเนินการผ่านวงล้อของ PDCA ประกอบไปด้วย 14 ข้อกำหนด ในแต่ละข้อกำหนดจะประกอบไปด้วย 4 มิติ ได้แก่
ㆍContent : การจัดทำขั้นตอนการปฏิบัติงานที่เป็นลายลักษณ์อักษร
ㆍDeployment : การสื่อสารขั้นตอนการปฏิบัติงานไปยังผู้ปฏิบัติอย่างมีประสิทธิภาพ
ㆍConformant : การปฏิบัติตามคู่มือและขั้นตอนการปฏิบัติอย่าง
ㆍPerformance : ประสิทธิผลของการดำเนินการถูกต้อง
โครงสร้างการบริหารงานด้านความปลอดภัย อาชีวอนามัยและสิ่งแวดล้อมองค์กร
1) ระดับกลุ่มบริษัทฯ: พีที่จี ได้จัดตั้งคณะกรรมการกำกับดูแลทางด้านนโยบายบริหารความมั่นคง ความปลอดภัย อาชีวอนามัยและสิ่งแวดล้อม โดยมีประธานเจ้าหน้าบริหารและกรรมการผู้จัดการใหญ่เป็นประธาน มีกรรมการผู้จัดการจากบริษัทฯในกลุ่มเป็นกรรมการและมีฝ่ายความปลอดภัยและสิ่งแวดล้อมเป็นเลขานุการ ในการดำเนินงาน บทบาทหน้าที่ เพื่อกำหนดทิศทางการบริหารจัดการความมั่นคง ความปลอดภัย อาชีวอนามัย และสิ่งแวดล้อมภายในกลุ่มบริษัทฯ ให้เป็นไปในทิศทางเดียวกันทั่วทั้งองค์กร
2) ระดับกลุ่มธุรกิจ: พีที่จี ได้บรรจุวาระการประชุมทางด้านความมั่นคง ความปลอดภัย อาชีวอนามัย และสิ่งแวดล้อม ให้เป็นส่วนหนึ่งของการประชุมฝ่ายปฏิบัติการ ประจำเดือน เพื่อให้ทีมผู้บริหารระดับกลางในสายงานปฏิบัติการได้มีส่วนร่วมในการทำกิจกรรมส่งเสริมความปลอดภัย และเป็นผู้นำในการทำกิจกรรมส่งเสริมความปลอดภัย ประจำพื้นที่
3) ระดับพื้นที่ปฏิบัติการ: พีทีจี ได้จัดให้ทุกพื้นที่ปฏิบัติการมีคณะกรรมการความปลอดภัยในการทำงานตามกฎหมาย เพื่อเป็นทีมในการบริหารจัดการทางด้านความมั่นคง ความปลอดภัย อาชีวอนามัย และสิ่งแวดล้อมประจำพื้นที่ และติดตามข้อเสนอแนะจากพนักงาน ติดตามความคืบหน้าประเด็นปัญหาทางด้านความปลอดภัยจากพนักงาน ตลอดจนวางแผนและเป็นผู้นำในการทำกิจกรรมส่งเสริมความปลอดภัยฯ
การประเมินความเสี่ยงด้านความปลอดภัย อาชีวอนามัย และสิ่งแวดล้อม
พีทีจี พิจารณากำหนดการชี้บ่งอันตราย การระบุประเด็นปัญหาด้านสิ่งแวดล้อม การประเมินความเสี่ยงและโอกาส ด้านความปลอดภัย อาชีวอนามัย และสิ่งแวดล้อม ที่เกี่ยวข้องกับกระบวนการปฎิบัติงาน การผลิตผลิตภัณฑ์และบริการโดยพิจารณามุมองวัฎจักรชีวิต (Life cycle) การเปลี่ยนแปลงหรือการปรับเปลี่ยนกิจกรรมในสภาวะปกติและไม่ปกติ รวมถึงสภาวะฉุกเฉิน ดังนี้
● การระบุอันตราย (Hazard identification)
บริษัทได้จัดทำกระบวนการเพื่อระบุอันตรายที่มีในระบบการจัดการ
โดยกระบวนการนี้บริษัทได้พิจารณาถึง วิธีการปฎิบัติงาน, ปัจจัยทางสังคม, การได้รับผลกระทบเชิงลบจากการร่วมเป็นที่ปรึกษา
ภาวะผู้นำและวัฒนธรรมองค์กร กิจกรรมและสถานการณ์แบบประจำหรือไม่ประจำ
รวมถึงอันตรายที่เกิดจาก โครงสร้างพื้นฐาน วัสดุอุปกรณ์ เป็นต้น
โดยฝ่ายความปลอดภัยและสิ่งแวดล้อมได้นำผลการบ่งชี้อันตรายมาปรับใช้ และปรับปรุงการบริหารจัดการด้านความปลอดภัยและอาชีวอนามัย
โดยในกระบวนการประเมินความเสี่ยงจัดให้มีการประเมินให้ครอบคลุมทั้งด้านความมั่นคง
ความปลอดภัย อาชีวอนามัย และสิ่งแวดล้อม ในทุกกระบวนการของการดำเนินการ
● การประเมินความเสี่ยงด้านสุขภาพ และโปรแกรมด้านสุขภาพ
บริษัท ได้ทำจัดกระบวนการประเมินความเสี่ยงด้านสุขภาพ โดยกระบวนการนี้บริษัทได้พิจารณาถึงปัจจัยเสี่ยงต่าง ๆ ที่พนักงานต้องสัมผัส ระยะเวลาการสัมผัส และมาตรการป้องกันที่มีอยู่ในปัจจุบัน ประกอบกับการกำหนดแผนการตรวจสุขภาพพนักงาน ทั้งกรณีเข้าปฏิบัติงานใหม่, เปลี่ยนแปลงการทำงานที่มีผลกระทบต่อปัจจัยเสี่ยงที่แตกต่างไปจากเดิม, ตรวจสุขภาพประจำปี และตรวจสุขภาพตามลักษณะงานที่มีความเสี่ยงเฉพาะอื่น ๆ เช่น งานอับอากาศ งานขับรถขนส่งวัตถุอันตราย เป็นต้น เพื่อให้มั่นใจว่าพนักงานมีสุขภาพที่ดี เหมาะสมกับสภาพแวดล้อมในการทำงาน และกรณีพบว่ามีความเสี่ยงด้านสุขภาพ ได้พิจารณามาตรการควบคุม และมาตรการลดความเสี่ยงได้ทันที ก่อนที่พนักงาน หรือผู้เกี่ยวจะได้รับผลกระทบต่อสุขภาพจากการปฏิบัติงาน
● การรายงานเกี่ยวกับอันตรายและความปลอดภัยที่เกี่ยวข้องกับการทำงาน
พีทีจี ได้ทำระบบในการรายงานการประเด็นทางด้านความมั่นคง ความปลอดภัย อาชีวอนามัยและสิ่งแวดล้อม ซึ่งแบ่งเป็นประเภทของการรายงานดังต่อไปนี้
1. การรายงานอุบัติเหตุและอุบัติการณ์ ในการทำงาน : เมื่อเกิดอุบัติเหตุเกิดขึ้นพนักงานต้องรายงานให้ผู้บังคับบัญชาและเจ้าหน้าที่ความปลอดภัยในการทำงานประจำพื้นที่ให้รับทราบทันที ผ่านช่องทางที่กำหนด จากนั้นจะต้องเข้าสู่กระบวนการสืบสวนหาสาเหตุที่แท้จริงเพื่อนำไปสู่การป้องกันและแก้ไข เพื่อไม่ให้เกิดซ้ำตามกระบวนการของบริษัทฯ ทั้งนี้ ได้มีการติดตามผลการดำเนินการแก้ไขป้องกันจากการสอบสวนอุบัติเหตุ โดยผ่านทางที่ประชุมคณะกรรมการความปลอดภัยฯ ประจำพื้นที่
2. การรายงานการกระทำที่ไม่ปลอดภัยและสภาพแวดล้อมในการทำงานที่ไม่ปลอดภัย : เมื่อพนักงานพบเห็นสภาพการณ์การทำงานที่ไม่ปลอดภัย สามารถรายงานผ่านโปรแกรม (Safety PT Service) เพื่อเข้าสู่กระบวนการวิเคราะห์และดำเนินการแก้ไข และมีการติดตามผล โดยผ่านทางที่ประชุมคณะกรรมการความปลอดภัยฯ ประจำพื้นที่
3. การรายงานสิ่งที่ไม่เป็นไปตามข้อกำหนดและกฎหมายจากการตรวจประเมินภายใน : พีทีจี ได้จัดให้มีการตรวจประเมินภายในทางด้าน SSHE ตามระบบการบริหารจัดการความมั่นคง ความปลอดภัย อาชีวอนามัย และสิ่งแวดล้อม กลุ่มบริษัท พีทีจี และมาตรฐานสากล โดยมีการตรวจประเมินระบบอย่างน้อยปีละ 1 ครั้ง และมีกระบวนการในการติดตามแก้ไขผ่านกระบวนการออก Non-conformity Report
พีทีจี ได้จัดทำนโยบายการให้สิทธิพนักงานในการหยุดงานเมื่อพบว่าพื้นที่การปฏิบัติงานไม่มีความปลอดภัย ( Stop Work Authority) ซึ่งนโยบายฉบับนี้ได้เป็นส่วนหนึ่งของ วัฒนธรรมความปลอดภัยของกลุ่ม พีทีจี " Stop if Unsafe " ซึ่งได้มีการส่งเสริมให้เกิดการนำไปปฏิบัติที่แท้จริงในส่วนปฏิบัติการคลังน้ำมัน ขนส่ง ซึ่งเริ่มจากการที่บริหารให้ความสำคัญและจริงจังตามนโยบาย( Stop Work Authority) โดยปฏิบัติตนเป็นแบบอย่างที่ดี ตามข้อกำหนด "การเป็นผู้นำด้านความปลอดภัย ( Visible Leadership)" ในส่วนของพนักงานและผู้รับเหมาต้องมีส่วนในการหยุดปฏิบัติงานทันทีและแจ้งให้หัวหน้างานรับทราบ เมื่อพบว่าไม่ปลอดภัย ทั้งนี้บริษัทฯ ได้จัดให้มีการให้รางวัลสำหรับพนักงานที่ปฏิบัติได้อย่างน่าชื่นชม ( Safety Bonus) และ มีการกำหนดโทษสำหรับคนที่ฝ่าฝืนกฎความปลอดภัย
พีทีจี ได้จัดให้มีการกระบวนการในการรายงานและสอบสวนสาเหตุของการเกิดอุบัติเหตุและอุบัติการณ์ในการปฏิบัติงาน ตามข้อกำหนดของ ISO 45001 :2018 โดยกระบวนการสอบสวนดำเนินการโดยคณะกรรมการที่มีความเชี่ยวชาญเฉพาะด้าน และใช้เครื่องมือในการสอบสวนที่เป็นสากล ที่ช่วยให้สามารถค้นหาสาเหตุที่แท้จริงของการเกิดเหตุ พร้อมกับมุ่งเน้นที่จะแก้ไขในเชิงระบบ หลังจากที่มีการสอบสวนสิ้นสุด เจ้าหน้าที่ความปลอดภัยระดับวิชาชีพประจำพื้นที่จะทำหน้าที่ในการติดตามประเด็นการแก้ไขจากการสอบสวน และ ทำการทบทวนผลการประเมินความเสี่ยงในทุกด้านๆ เพื่อป้องกันไม่ให้เกิดเหตุการณ์ซ้ำอีกในพื้นที่อื่น
ผลการประเมินความเสี่ยงในปี 2567
พีทีจีดำเนินการประเมินและทบทวนความเสี่ยงด้านอาชีวอนามัย ความปลอดภัย และสิ่งแวดล้อมในทุกกิจกรรมและทุกพื้นที่อย่างต่อเนื่อง โดยให้ความสำคัญกับการทบทวนมาตรการควบคุมและลดความเสี่ยงอย่างน้อยปีละหนึ่งครั้ง เพื่อให้มั่นใจว่าการดำเนินงานเป็นไปอย่างปลอดภัยและสอดคล้องกับมาตรฐานที่กำหนด ในปี 2567 บริษัทฯ ได้ดำเนินการประเมินความเสี่ยงในสองประเด็นหลัก ได้แก่ ความเสี่ยงด้านความปลอดภัย และ ความเสี่ยงด้านสิ่งแวดล้อม ซึ่งผลการประเมินพบว่า
การดำเนินงานเพื่อพัฒนาคุณภาพด้านความปลอดภัย อาชีวอนามัย และสิ่งแวดล้อมองค์กร
พีทีจี จัดตั้งคณะกรรมการกำกับดูแลนโยบายบริหารความมั่นคง ความปลอดภัย อาชีวอนามัยและสิ่งแวดล้อมของกลุ่มบริษัทฯ เพื่อกำหนดทิศทางการบริหารจัดการความมั่นคง ความปลอดภัย อาชีวอนามัยและสิ่งแวดล้อมภายในกลุ่มบริษัทฯ ให้เป็นไปในทิศทางเดียวกัน โดยคณะกรรมการนี้ประกอบด้วย ประธานเจ้าหน้าบริหารและกรรมการผู้จัดการใหญ่ เป็นประธานและมี กรรมการผู้จัดการจากบริษัทฯในกลุ่ม เป็นกรรมการ และมี ฝ่ายความปลอดภัยและสิ่งแวดล้อมเป็นเลขาณุการในการดำเนินงาน
พีทีจี จัดตั้งฝ่ายความปลอดภัยและสิ่งแวดล้อม เพื่อดูแลบริหารจัดการงานด้านความปลอดภัยในการทำงานและพัฒนาผลการดำเนินงานด้านอาชีอนามัยและสิ่งแวดล้อมให้สอดคล้องตามกฏหมาย และมาตรฐานระดับสากล เพื่อลดผลกระทบที่อาจเกิดขึ้นต่อผู้มีส่วนได้เสียจากการดำเนินธุรกิจ ในการพัฒนาระบบความปลอดภัย อาชีวนามัย และสิ่งแวดล้อม บริษัทปฏิบัติตามและดำเนินการขอการรับรองตามมาตรฐานสากล ISO14001 : 2015 & ISO45001 : 2018 ในขอบเขตของ กระบวนการ รับ จัดเก็บ และจ่ายผลิตภัณฑ์น้ำมันเชื้อเพลิงภายในคลังน้ำมัน เพื่อเป็นต้นแบบในการพัฒนาปรับปรุงระบบการจัดการและพัฒนาบุคลากรไปพร้อมกัน ซึ่งในอนาคตอันใกล้จะมีการขยายขอบเขตให้ครอบคลุมทุกกระบวนการและคลังน้ามัน ฝ่ายความปลอดภัยและสิ่งแวดล้อม มุ่งมั่นเพิ่มศักยภาพขององค์กรในด้านความปลอดภัยในทุกกิจกรรมของธุรกิจตลอดห่วงโซ่อุปทาน โดยมีการริเริมและปรับปรุงกระบวนการทำงานให้มีประสิทธิภาพและเกิดความปลอดภัยอย่างต่อเนื่อง เพื่อขับเคลื่อน พีทีจี สู่องค์กรแห่งความเป็นเลิศ (Transform) ดังนี้
- การบริหารจัดการความมั่นคง ความปลอดภัย อาชีวอนามัยและสิ่งแวดล้อม คลังน้ำมัน
ฝ่ายความปลอดภัยและสิ่งแวดล้อมมุ่งพัฒนาระบบการบริหารจัดการความมั่นคง ความปลอดภัย อาชีวอนามัยและสิ่งแวดล้อม ให้สอดคล้องตามกฎหมายและมาตรฐานสากล โดยคลังน้ำมัน มีการพัฒนาระบบการบริหารจัดการความมั่นคง ความปลอดภัย อาชีวอนามัยและสิ่งแวดล้อม ของกลุ่มบริษัท พีทีจี ( PTG SSHEMS) มาประยุกต์ใช้ เป็นพื้นฐาน และจัดทำระบบการบริหารจัดการอาชีวอนามัยและความปลอดภัยตามมาตรฐานสากล ( ISO 45001: 2018) ทั้งนี้ได้มีการกำหนดวัตถุประสงค์เป้าหมายทางด้านความมั่นคง ความปลอดภัยอาชีวอนามัย และสิ่งแวดล้อม ให้เป็นไปตามมาตรฐานสากล และเป็นกรอบการดำเนินโครงการภายในคลังน้ำมัน
พีทีจี จัดให้พนักงานเข้ามามีส่วนร่วมในการกำหนดกิจกรรมส่งเสริมความปลอดภัย ภายในคลังน้ำมัน เช่น โครงการปรับปรุงพื้นที่การปฏิบัติงานของพนักงานโดยการนำหลักการประเมินทางการยศาสตร์ มาประยุกต์ใช้ (คลังน้ำมันแม่กลอง) โครงการปรับปรุงคลังสินค้าโดยใช้หลักการ 5ส ( คลังน้ำมันขอนแก่น) ซึ่งได้รับรางวัล Kaizen Award ระดับประเทศ นอกจากนี้ในทุกคลังน้ำมันได้จัดให้มี เจ้าหน้าที่ความปลอดภัยในการทำงานประจำพื้นที่ที่มีคุณสมบัติตามที่กฎหมายกำหนด ได้แก่ 1) เจ้าหน้าที่ความปลอดภัยระดับบริหาร ( ผู้บริหารทุกคน) 2) เจ้าหน้าที่ความปลอดภัยในการทำงานระดับหัวหน้างาน ( พนักงานระดับหัวหน้างานทุกคน) 3) เจ้าหน้าที่ความปลอดภัยระดับวิชาชีพ ประจำคลัง ทั้งนี้ทุกคลังน้ำมันได้จัดให้มีคณะกรรมการความปลอดภัยในการทำงาน (คปอ.) ที่ทำหน้าที่เป็นตัวแทนของพนักงานในการบริหารจัดการทางด้านความมั่นคง ความปลอดภัย อาชีวอนามัยและสิ่งแวดล้อม ประจำพื้นที่ รวมถึงวางแผนจัดกิจกรรมส่งเสริมความปลอดภัยฯ ภายในคลังน้ำมัน ภายใต้กรอบการบริหารจัดความมั่นคง ความปลอดภัย อาชีวอนามัย และสิ่งแวดล้อม ของกลุ่มบริษัทฯ
ทั้งนี้เพื่อเป็นการเตรียมความพร้อมต่อภาวะฉุกเฉินและภาวะวิกฤต ทุกคลังน้ำมันได้มีการจัดทำแผนตอบโต้ภาวะฉุกเฉินและภาวิกฤต เพื่อให้มั่นใจว่าจะสามารถระงับเหตุได้อย่างถูกต้องและรวดเร็ว เพื่อลดความสูญเสียที่อาจเกิดขึ้นกับคลังน้ำมัน ชุมชน และ สิ่งแวดล้อมโดยรอบคลังน้ำมัน และจัดให้มีการฝึกซ้อมอย่างน้อยปีละ 1 ครั้งในทุกแผน และปรับปรุงพัฒนาแผนให้สอดรับกับการเปลี่ยนแปลงที่เกิดขึ้นทั้งจากภายในและภายนอกคลังน้ำมัน
- การตรวจสอบและอบรมด้านความปลอดภัยในสถานีบริการ
ฝ่ายความปลอดภัยและสิ่งแวดล้อม ได้ตระหนักถึงความปลอดภัยของลูกค้าที่เข้ามาใช้บริการของสถานีบริการภายใต้แบนด์ PT โดยได้มีการดําเนินการตรวจสอบความปลอดภัยภายในครอบคลุมทุกธุรกิจในสถานีบริการเพื่อค้นหาความเสี่ยงและสาเหตุของอันตรายต่าง ๆ ที่มีแนวโน้มจะก่อให้เกิดผลกระทบต่อความปลอดภัย อาชีวอนามัยของพนักงานและลูกค้าที่ใช้บริการ หรืออาจก่อให้เกิดความเสียหายต่อทรัพย์สินของบริษัทและลูกค้า ซึ่งอาจเกิดขึ้นได้ในทุกส่วนของสถานีบริการ เช่น ภายในตัวอาคารลานจ่าย ตู้จ่ายน้ำมัน โดยฝ่ายความปลอดภัยและสิ่งแวดล้อมจะนําข้อมูลอันตราย ที่ได้มาแก้ไข ปรับปรุง และระบุมาตรการป้องกันก่อนที่จะเกิดอุบัติเหตุ (Accident) หรืออุบัติการณ์ (Incident) ขึ้นในสถานีบริการ รวมถึงรายงานต่อคณะกรรมการความปลอดภัยและสิ่งแวดล้อมของบริษัทต่อไป และติดตามการดำเนินการแก้ไขจนกระทั่งดำเนินการแล้วเสร็จ ทั้งนี้ได้มีการนำประเด็นความเสี่ยงระดับสูงและสูงมากรายงานให้ผู้บริหารรับทราบและดำเนินการแก้ไขอย่างเร่งด่วนต่อไป ภายใต้คณะกรรมการบริหารความเสี่ยงองค์กร
ในจัดทำรายงานข้อมูลการตรวจสอบ และติดตามการแก้ไขปัญหาด้านความปลอดภัยและสิ่งแวดล้อมในสถานีบริการ ฝายความปลอดภัยและสิ่งแวดล้อมใช้ระบบ Power BI เพื่อช่วยในการวิเคราะห์ข้อมูลธุรกิจในเชิงลึก โดยสามารถบริหารข้อมูลผ่าน Dashboard ได้แบบ Real time โดยมีการให้ระบบได้ทํางานร่วมกับโปรแกรมการออกแบบการตรวจความปลอดภัยและสิ่งแวดล้อมสถานีบริการ (Safety PT Service) เพื่อประยุกต์ใช้ในการดําเนินธุรกิจได้อย่างคล่องตัว นอกจากนี้ยังสามารถลดเวลาในการทํางานของพนักงาน รวมทั้งลดปริมาณการใช้กระดาษร้อยละ 100 และสามารถกําหนดสิทธิ์การเข้าถึงข้อมูลสําหรับผู้ใช้งานได้ ทําให้มีความปลอดภัยในการใช้ข้อมูลสูง
นอกจากนี้ บริษัทได้จัดทำแผนการจัดการและลดความเสี่ยงในการขยายตัวของธุรกิจ และขยายสาขาใหม่ โดยมีการชี้บ่งอันตราย การประเมินโอกาส และการประเมินความเสี่ยงทุกกิจกรรมและทุกสภาพแวดล้อมในสถานที่ทำงานและบริเวณ ใกล้เคียง ที่ได้รับผลกระทบจากกิจกรรมของบริษัทในการทำงานของพนักงานทุกระดับ เพื่อให้ทราบถึงอันตรายที่มีอยู่ทั้งหมดจากการทำงานและจากพื้นที่หรือสภาพแวดล้อมในการทำงานโดยมีการจัดลำดับความเสี่ยงที่ได้จากการประเมินความเสี่ยงทั้งหมด รวมทั้งฝ่ายความปลอดภัยและสิ่งแวดล้อมได้สร้างความตระหนักและการมีส่วนร่วมของพนักงานในการบริหารจัดการด้านความปลอดภัยฯ ผ่านกิจกรรมส่งเสริมความปลอดภัย เช่น โครงการ Safety Clinic ที่จะเป็นการให้ความรู้และสร้างความตระหนักให้กับพนักงานที่ปฏิบัติงานในสถานีบริการ เพื่อให้มั่นใจว่า พนักงานจะปฏิบัติงานด้วยความอยู่ดี มีสุข
- การบริหารจัดการความมั่นคง ความปลอดภัย อาชีวอนามัยและสิ่งแวดล้อม ขนส่ง การตรวจสอบและอบรมด้านความปลอดภัยสำหรับรถขนส่งน้ำมัน
ฝ่ายความปลอดภัยและสิ่งแวดล้อม ได้เล็งเห็นความสำคัญของความปลอดภัยจากการขนส่งน้ำมันพีที ที่สดใหม่ทุกวัน ฝ่ายความปลอดภัยฯ ได้มีการมอบหมายพนักงานที่ทำหน้าที่เป็นเจ้าหน้าที่ความปลอดภัยในการทำงานประจำธุรกิจขนส่ง เพื่อวางแผน พัฒนา ระบบมาตรฐานการบริหารจัดการความมั่นคง ความปลอดภัย อาชีวอนามัย และสิ่งแวดล้อม ของการขนส่งผลิตภัณฑ์ของบริษัทฯ ภายใต้กรอบการบริหารจัดการของระบบ PTG SSHEMS
พีทีจี ได้มีการกำกับดูแล บริษัท พีทีจี โลจิสติกส์ จำกัด ซึ่งเป็นบริษัทในกลุ่ม ให้ดำเนินกิจกรรมที่เกี่ยวข้องกับการบริหารจัดการความมั่นคง ความปลอดภัย อาชีวอนามัย และสิ่งแวดล้อม ให้สอดคล้องกับกลุ่มบริษัทฯ โดยมีการกำหนดนโยบายความมั่นคง ความปลอดภัย อาชีวอนามัยและสิ่งแวดล้อมที่สอดคล้องกับกลุ่มบริษัทฯ และจัดให้มีการคณะกรรมการความปลอดภัยในการทำงานประจำพื้นที่ เพื่อกำหนดและวางแผนในการบริหารจัดการความมั่นคง ความปลอดภัย อาชีวอนามัย และสิ่งแวดล้อม เพื่อให้มั่นใจจะสามารถป้องกันไม่ให้เกิดอุบัติเหตุจากการขับขี่รถขนส่งผลิตภัณฑ์
พีทีจี ได้จัดให้มีศูนย์ฝึกอบรมในการขับขี่ปลอดภัยให้กับพนักงานขับรถขนส่งผลิตภัณฑ์ เพื่อให้มั่นใจได้ว่าพนักงานขับรถขนส่งผลิตภัณฑ์ จะไม่เกิดอุบัติเหตุและทำให้เกิดผลกระทบกับผู้มีส่วนได้เสีย โดยรวม ภายใต้โครงการ “สุภาพบุรุษพีทีจี : มีวินัย มีน้ำใจ ไม่เห็นแก่ตัว” ที่มุ่งปลุกฝังจิตสำนึกทางด้านความปลอดภัยในการขับขี่ให้กับพนักงาน นอกจากนี้ พีทีจี ได้นำระบบ AI มาใช้ในการตรวจจับความผิดปกติของพนักงานขับรถขนส่งผลิตภัณฑ์ เพื่อให้มั่นใจว่าพนักงาขับรถมีความพร้อมในการปฏิบัติงาน พร้อมกับมีการสุ่มตรวจสารเสพติดและแอลกอฮอล์ อยู่เสมอทั้งนี้ ได้จัดให้มีนโยบายในการป้องกันการใช้สารเสพติด และ กัญชา ภายในบริษัทฯ โดยพิจารณาความเหมาะสมและความปลอดภัยของพนักงานขับรถตามนโยบายของภาครัฐ
- การส่งเสริมความปลอดภัยให้แก่ผู้รับเหมา
- การสื่อสารข้อกําหนดด้านความปลอดภัยในการคัดเลือกบริษัทผู้รับเหมาของสถานีบริการที่มีการให้บริการเชิงพาณิชย์ (Model A)
ฝ่ายความปลอดภัยและสิ่งแวดล้อมได้จัดให้มีหน่วยงานที่ควบคุมกำกับดูแลทางด้านความมั่นคง ความปลอดภัย อาชีวอนามัยและสิ่งแวดล้อมของผู้รับเหมา โดยในกระบวนการควบคุมกำกับดูแลทางด้านความปลอดภัยของผู้รับเหมามีการดำเนินการดังต่อไปนี้
- การจัดทําและสื่อสารข้อบังคับด้านความปลอดภัยสําหรับผู้รับเหมา
ฝ่ายความปลอดภัยและสิ่งแวดล้อมได้จัดทําคู่มือว่าด้วยความปลอดภัยในการทํางานสําหรับการควบคุมการปฏิบัติงานที่มีความเสี่ยงสําหรับผู้รับเหมา เพื่อให้ผู้รับเหมาที่เข้ามาดําเนินงานก่อสร้างให้กับกลุ่มบริษัท ได้ใช้เป็นแนวทางในการดําเนินการเกี่ยวกับความปลอดภัยและสภาพแวดล้อมในการทํางาน โดยสามารถนําไปปฏิบัติได้ถูกต้องครบถ้วนตามที่กฎหมายกําหนด รวมถึงการรายงานการเกิดอุบัติเหตุ ของผู้รับเหมาให้บริษัททราบ ซึ่งคู่มือฉบับนี้ครอบคลุมผู้รับเหมาที่เข้ามาดําเนินงานก่อสร้างในขอบเขต สถานีบริการน้ำมัน LPG ร้านค้าสะดวกซื้อ Max Mart ร้านกาแฟพันทธ์ไทย Coffee World Autobac Protruck จุดบริการ Max Camp และกลุ่มบริษัทขนส่งน้ำมันและก๊าซปิโตรเลียมเหลว
ผลการดำเนินงานในปี 2567
- การป้องกันผลกระทบและอันตรายจากการดำเนินธุรกิจต่อชุมชน
ฝ่ายความปลอดภัยและอาชีวอนามัยจัดทําประชาพิจารณ์ เพื่อรับฟังความคิดเห็นของประชาชนที่เกี่ยวข้องรวมถึงชุมชนในบริเวณใกล้เคียงสถานีบริการน้ำมัน เชื้อเพลิง และสถานีบริการจําหน่ายก๊าซปิโตรเลียมเหลวแห่งใหม่ที่จะเปิดในทุก ๆ สาขา โดยมีขั้นตอน ดังนี้
- จัดทําข้อมูลและควบคุมการก่อสร้างเพื่อสร้างความมั่นใจด้านความปลอดภัยระหว่างการจัดตั้งสถานีบริการ โดยจัดให้มีการกั้นเขตพื้นที่การก่อสร้างสถานีให้ชัดเจน อุปกรณ์ป้องกันอันตรายส่วนบุคคล (PPE) ในการทํางาน จัดให้มีเจ้าหน้าที่ความปลอดภัยในการทํางานประจําพื้นที่เขตก่อสร้าง ตรวจสอบการทํางานด้านความปลอดภัยในการทํางานของผู้รับเหมา กรณีผู้รับเหมาทํางานที่มีความเสี่ยงที่เป็นอันตราย ผู้รับเหมาต้องมีการนําส่งแผนฉุกเฉินของบริษัทผู้รับเหมา จัดเตรียมความพร้อมถังดับเพลิงไว้ตามจุดต่างๆ ในสถานที่ทํางานที่เกี่ยวข้องกับงานที่อาจก่อให้เกิดประกายไฟเพื่อระงับเหตุเบื้องต้น
เป้าหมายการดำเนินงาน
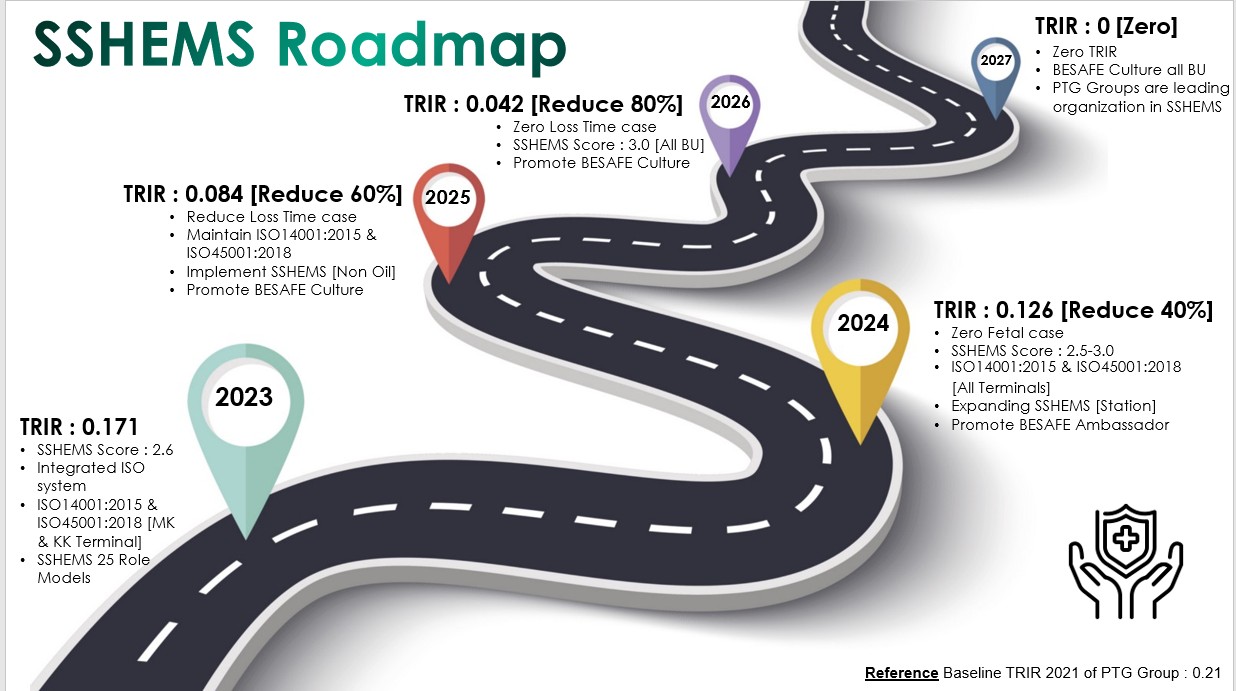
ตัวชี้วัด | ผลการดำเนินงาน | เป้าหมาย | |||
2565 | 2566 | 2567 | 2567 | 2570 | |
อัตราการบาดเจ็บจากการทำงานรวม
(Total Recordable Injuries Rate: TRIR) ต่อ หนึ่งล้านชั่วโมงการทำงานของพนักงาน* |
0.71 | 0.86 | 0.67 | 0.63 | 0.315 |
จำนวนพนักงาน/ผู้รับเหมาเสียชีวิตจากการปฏิบัติงาน (ราย) | พนักงาน 1 ราย ผู้รับเหมา 0 ราย |
พนักงาน 1 ราย ผู้รับเหมา 0 ราย |
พนักงาน 0 ราย ผู้รับเหมา 0 ราย |
0 | 0 |
อัตราความถี่ของการบาดเจ็บจากการทำงานถึงขั้นหยุดงาน (Lost Time Injury Frequency Rate: LTIFR) ต่อหนึ่งล้านชั่วโมงการทำงาน ของพนักงานและผู้รับเหมา |
พนักงาน 0.69 ผู้รับเหมา 0.8 |
พนักงาน 0.69 ผู้รับเหมา 0.54 |
พนักงาน : 0.605 ผู้รับเหมา : 0.45 |
พนักงาน 0.552 ผู้รับเหมา 0 |
พนักงาน 0.276 ผู้รับเหมา 0 |
อัตราความถี่ของการเจ็บป่วยและโรคจากการทำงาน (Occupational Illness Frequency Rate:OIFR) ต่อหนึ่งล้านชั่วโมงการทำงาน ของพนักงาน |
0 | 0 | 1 | 0 | 0 |
หมายเหตุ:
- ข้อมูลการเสียชีวิตจากการทำงาน อัตราความถี่ของการบาดเจ็บจากการทำงานถึงขั้นหยุดงาน และอัตราความถี่ของการเจ็บป่วยด้วยโรคจากการทำงานครอบคลุมกลุ่มบริษัท พีทีจี เอ็นเนอยี
- อัตราการบาดเจ็บจากการทำงานรวม ครอบคลุมสถานปฏิบัติการของบริษัท PTG, MSS, MAX, PTGGE, PTGLG, ATL, PTC, OLP, MaxMart, PUN, SAB, คลังน้ำมัน, ศูนย์กระจายสินค้า
ดาวน์โหลดความมุ่งมั่นด้านความปลอดภัย อาชีวอนามัย และสภาพแวดล้อมในการทำงาน
มาตรการป้องกันเพื่อควบคุมการเกิดอุบัติเหตุ และการเจ็บป่วยจากการทำงาน
กลุ่ม บริษัท พีทีจี เอ็นเนอยี มีการขยายตัวของธุรกิจ ส่งผลให้มีธุรกิจใหม่ ๆ และจำนวนพนักงานภายในองค์กรเพิ่มขึ้นอย่างต่อเนื่อง แต่อย่างไรก็ตาม เพื่อให้เกิดความปลอดภัยในการทำงานของพนักงาน ผู้รับเหมา รวมถึงป้องกันผลกระทบที่อาจเกิดกับผู้มาติดต่อ ชุมชน และผู้มีส่วนได้ส่วนเสียอื่น บริษัทฯ จึงมีการกำหนดมาตรการป้องกันเพื่อควบคุมการเกิดอุบัติเหตุ และการเจ็บป่วยจากการทำงานของกลุ่มบริษัท พีทีจี เอ็นเนอยี ไว้ดังนี้
1. การศึกษาข้อมูลมาตรฐานการปฏิบัติงานด้านความมั่นคง ความปลอดภัย อาชีวอนามัย และสิ่งแวดล้อม และวางแผนการปฏิบัติให้สอดคล้องตามที่กฎหมาย พันธะสัญญา และมาตรฐานสากลที่เกี่ยวข้องกำหนด
2.การประยุกต์ใช้ระบบมาตรฐานด้านความมั่นคง ความปลอดภัย อาชีวอนามัย และสิ่งแวดล้อม ภายในองค์กร ไม่ว่าจะเป็น ระบบบริหารจัดการด้านคุณภาพ (ISO9001:2015), ระบบบริหารจัดการด้านสิ่งแวดล้อม (ISO14001:2015), ระบบการจัดการความปลอดภัยทางถนนและการจราจร (ISO39001), ระบบบริหารจัดการด้านอาชีวอนามัยและความปลอดภัย (ISO45001:2018), การจัดการความปลอดภัยกระบวนการผลิต (Process Safety Management: PSM) และการจัดทำระบบมาตรฐานด้านความมั่นคง ความปลอดภัย อาชีวอนามัย และสิ่งแวดล้อม (PTG SSHEMS)
3.การกำหนดนโยบายคุณภาพ ความมั่นคงปลอดภัย อาชีวอนามัย และสิ่งแวดล้อม กลุ่มบริษัท พีทีจี เอ็นเนอยี เพื่อเป็นแนวทางในการปฏิบัติงานด้านคุณภาพ ความมั่นคงปลอดภัย อาชีวอนามัย และสิ่งแวดล้อมภายในองค์กร แสดงถึงความมุ่นมั่นในการกำกับดูแล การบำรุงรักษา การเพิ่มประสิทธิผลให้ดีขึ้นอย่างต่อเนื่อง
4.การกำหนดเป้าหมายด้านความปลอดภัยและสิ่งแวดล้อมภายในกลุ่มบริษัทผ่านตัวชี้วัดด้านต่าง ๆ อีกทั้งบริษัทยังได้ดำเนินการติดตามและประเมินผลการดำเนินงานด้านสุขภาพและความปลอดภัยอย่างต่อเนื่องเป็นประจำทุกปี ซึ่งบริษัทได้มีการเปรียบเทียบผลการดำเนินงานกับกลุ่มธุรกิจประเภทเดียวกันในอุตสาหกรรม เพื่อใช้เป็นข้อมูลในการพัฒนาและปรับปรุงมาตรการด้านความปลอดภัยในสถานีบริการและหน่วยงานต่าง ๆ อย่างมีประสิทธิภาพ อาทิเช่น
a. อัตราการบาดเจ็บที่มีการส่งรักษาโรงพยาบาลขึ้นไป (TRIR) ครั้งต่อสองแสนชั่วโมง ลดลง 40% (เป้าหมาย TRIR ≤0.126) : ผลการดำเนินงานปี 2566 ค่า TRIR = 0.171 ซึ่งแสดงถึงว่าอัตราการเกิดอุบัติเหตุของกลุ่มบริษัท ไม่เป็นไปตามเป้าหมาย แต่เมื่อเทียบกับปีฐาน (TRIR ปี 2564 = 0.21) พบว่า ลดลง 18.57%
b. การตรวจประเมินระบบการจัดการ Safety Management System ตามข้อกำหนด PTG SSHEMS Score เป้าหมาย ≥2.5 คะแนนในทุกกลุ่มธุรกิจ ซึ่งผลการดำเนินงานปี 2566 คะแนนที่ประเมินได้ = 2.6 เป็นไปตามเป้าหมาย
c. การรับรองความยั่งยืนด้านความปลอดภัย และด้านสิ่งแวดล้อมของกลุ่มบริษัท พีทีจี เอ็นเนอยี ที่ได้รับการรับรองจากหน่วยงานภายนอก เป้าหมาย ≥ 8 การรับรอง ซึ่งผลการดำเนินงานปี 2566 รวมการรับรองที่กลุ่มบริษัท พีทีจี เอ็นเนอยีได้รับทั้งหมด 17 การรับรอง ไม่ว่าจะเป็น สถานประกอบการดีเด่นด้านความปลอดภัย, สำนักงานสีเขียว, การป้องกันและแก้ไขปัญหายาเสพติด, การรับรองการลดการปลดปล่อยก๊าซเรือนกระจก (LESS) เป็นไปตามเป้าหมาย
5. การจัดตั้งฝ่ายความปลอดภัยและสิ่งแวดล้อมเป็นหน่วยงานความปลอดภัย เพื่อกำกับดูแลงานด้านความปลอดภัย อาชีวอนามัย และสภาพแวดล้อมการทำงานภายในองค์กร
6. การจัดตั้งคณะกรรมการความปลอดภัยฯ ในแต่ละกลุ่มบริษัท เพื่อเป็นช่องหาการสื่อสารมาตรการระหว่างฝ่ายบริหาร และฝ่ายลูกจ้าง ในการร่วมกันพิจารณา และดำเนินงานด้านความปลอดภัย อาชีวอนามัย และสภาพแวดล้อมการทำงานภายในองค์กร
7. การฝึกอบรมความรู้ด้านความปลอดภัย อาชีวอนามัย และสิ่งแวดล้อมตามกฎหมาย ไม่ว่าจะเป็น หลักสูตรความปลอดภัย อาชีวอนามัย และสภาพแวดล้อมในการทำงานสำหรับพนักงานเข้าทำงานใหม่/เปลี่ยนงาน (Basic Safety), หลักสูตรดับเพลิงขั้นต้น (Basic Fire), หลักสูตรเจ้าหน้าที่ความปลอดภัยระดับบริหาร, หลักสูตรเจ้าหน้าที่ความปลอดภัยระดับหัวหน้างาน และหลักสูตรผู้ปฏิบัติงานต่างๆ ตามที่กรมธุรกิจพลังงานกำหนด
8. พัฒนาทักษะภาวะผู้นำด้านความปลอดภัยของผู้บริหารและหัวหน้างานให้เข้าใจภาพรวมของการบริหารจัดการความมั่นคงความปลอดภัย อาชีวอนามัยและสิ่งแวดล้อม เพื่อนำไปสู่การตัดสินใจและสร้างความเชื่อมั่นให้กับผู้ใต้บังคับบัญชา
9. การจัดทำข้อบังคับและคู่มือความปลอดภัย อาชีวอนามัย และสภาพแวดล้อมในการทำงาน ในแต่ละกลุ่มธุรกิจ
10. การสอบสวนอุบัติเหตุร่วมกับผู้เกี่ยวข้องให้ครอบคลุมทุกด้าน เพื่อค้นสาเหตุของการอุบัติเหตุที่เกิดขึ้น และกำหนดมาตรการในการแก้ไข/ป้องกัน เพื่อป้องกันการเกิดอุบัติเหตุซ้ำ และขยายผลไปยังพื้นที่ และกลุ่มกิจการอื่น ภายในองค์กรที่เกี่ยวข้อง
11. การสรุปสถิติข้อมูลอุบัติเหตุ รวมถึงข้องมูลด้านความปลอดภัย อาชีวอนามัย และสิ่งแวดล้อมที่เกิดขึ้นภายในองค์กร เพื่อนำมาวิเคราะห์แนวโน้มการเกิดอุบัติเหตุ และกำหนดกลยุทธ์การดำเนินงาน เพื่อจัดการความเสี่ยงที่อาจส่งผลให้เกิดการบาดเจ็บ/เจ็บป่วยจากการทำงาน / ความมั่นคงปลอดภัย / สิ่งแวดล้อม / ความปลอดภัยในกระบวนการผลิต
12. การศึกษาอุบัติการณ์ภายนอกองค์กร เพื่อนำมาวิเคราะห์ความเสี่ยงภายในองค์กร รวมถึงการกำหนดมาตรการป้องกันการเกิดอุบัติภัยร้ายแรงภายในองค์กร
13. การตรวจการปฏิบัติงาน และอุปกรณ์ด้านความปลอดภัย อาชีวอนามัย และสิ่งแวดล้อมในแต่ละพื้นที่ ผ่านรูปแบบต่างๆ เพื่อค้นหาความเสี่ยง และดำเนินการแก้ไขทันที เช่น การตรวจพื้นที่ปฏิบัติงานโดยหัวหน้างานเจ้าของพื้นที่, การตรวจความปลอดภัยโดยคณะกรรมการความปลอดภัยฯ ประจำเดือน, การตรวจพื้นที่สาขากลุ่มสถานีบริการ, ร้านจำหน่ายแก๊ส, ร้านกาแฟ, ร้านมินิมาร์ทโดยเจ้าหน้าที่ความปลอดภัย เป็นต้น
14. จัดกิจกรรมส่งเสริมความปลอดภัยฯ ที่ให้พนักงานมีส่วนร่วม เพื่อให้เกิดทักษะและการตระหนักรู้ในประเด็นความมั่นคง ความปลอดภัย อาชีวอนามัย และสิ่งแวดล้อม